E-commerce
The activity of online retailers has increased significantly over the past few years, thus signalizing a need for a more efficient order fulfillment. Running an e-commerce warehouse has very specific requirements, in order to properly manage challenges like next-day-delivery or returns.
Optimization of warehouse
Scalability and modularity
Space saving
This hyper-dynamic market requires highly efficient warehouse solutions. In most cases, this includes a manual area for pallets and boxes and an automated area, designed for piece-picking.
For newly planned warehouses, a highly automated solution is the cleverest approach, making the material flow and the workspace safer, but also significantly increasing throughput. In this case, replacing the manual area with a shuttle system for boxes or for pallets and connecting it via our conveyor systems to an AutoStore installation for the piece-picking area insures an optimal performance of the ensemble. Portal packaging robots or the Nomagic pick-robot, can also be added. Optimizing the user interface of the system with our LogiCS UI for the human-operated stations can further increase pick-performance by up to 90% (compared to a traditional manual picking-process). Not to mention that both AutoStore, and the picking robots can work around the clock, thus covering several shifts and buffering the weekend days.

The situation is a bit different when we are looking at an already existing warehouse and its predetermined conditions. Adding an AutoStore system has become almost a “must” for any e-commerce business, but that is gladly something that can be easily adapted to any preexisting warehouse, because of the immense flexibility that this system offers. However, adding shuttles and cobots might weight too heavy on the ROI in some cases. A numerous and experienced working team can provide good throughput in the manual- and order-consolidation areas. Furthermore, thanks to our LogiCS UI, the human workers can easily and error-free commission directly at the ergonomic AutoStore workstations. This hybrid solution has been in high-demand in our activity in the past few years and is a natural step forward.
E-commerce

We strongly believe that full-automation is the key to a future-proof warehouse, but our main goal remains that of supporting our customers in optimizing their logistics in a sustainable and efficient manner. So, every solution that we offer is the result of thorough analysis and tailor made planning, designed to address the highly individual challenges of each business.
AutoStore is a very exciting cube. It allowed us to achieve a 50% cost and process efficiency, compared to other automated warehousing solutions.
Olaf Koch, Logistic Manager – Tennis Point
Register
Please complete the form below to access this content. One of our specialists will get in touch with you shortly.
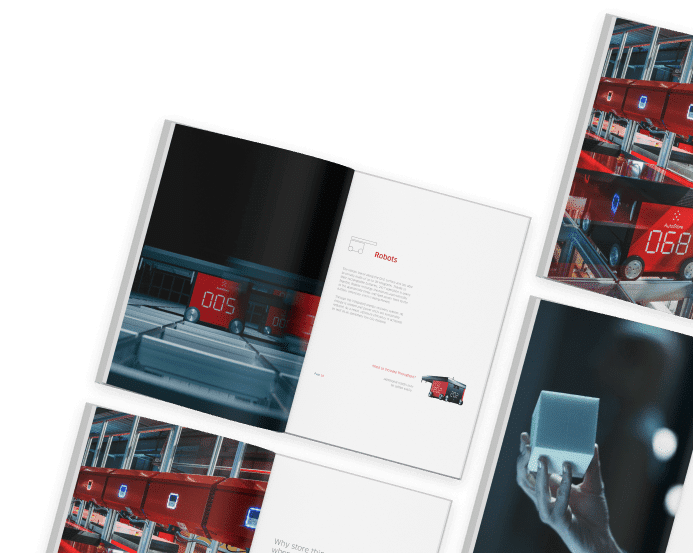
Thank you
Thank you for your registration! The requested files will be sent to you shortly.