Juncker Bike Parts -Over 300% more order lines per hour
Juncker Bike Parts is a distributor of bike parts and accessories for bike shops in the Netherlands, Belgium and Luxembourg. In addition to replacement parts they also sell the other products that bicycle shops stock, for example clothing.
“The leisure market is growing,” says Michiel Harmsen, Manager Operations at Juncker Bike Parts. “Bicycles are a green product and increasing numbers of people are cycling, some of them on sports or electric bikes.” Every day, three shifts work from 8 am to 10 pm to get all the order lines packed on time and delivered to the bicycle shop the next day.
New logistics centre in Apeldoorn
In 2015 Juncker Bike Parts relocated from Veenendaal to Apeldoorn. “In Veenendaal we had overgrown our premises,” says Harmsen. “The location in Apeldoorn came free which gave the possibility to set up a completely new logistics centre. Looking to process more order lines in fewer hours, a suitable system was sought. In Veenendaal when busy we started to pick up orders already by 8 in the morning. That meant that the orders that were placed later in the day had to be sent separately. In order to be able to combine all orders we started to look for a system that had enough capacity to process everything in a short time after the last order,” says Harmsen. Based on compactness and speed, Juncker Bike Parts came to the AutoStore system of LLS.
AutoStore as pleasant work environment
Midway through 2013, Juncker Bike Parts and LLS came together for talks. LLS advised Juncker Bike Parts first of all about the most efficient application of the system. Based on the available space and possibilities, LLS developed a completely new tunnel system under the AutoStore. Harmsen: “That produced new challenges such as lighting and noise reduction. As the products in a shop have to be promoted, these may not be damaged. That’s why it is very important that the employees are able to work with focus and without distractions. LLS has helped us a great deal in this with discussions and development. The eventual system has produced a work environment in which workers can work in an ergonomically sound manner, without any noise nuisance. Ordering later thanks to AutoStore Due to the enormous increase in the number of order lines per hour, the systemcan wait until the end of the day before picking orders. […]
Register
Please complete the form below to access this content. One of our specialists will get in touch with you shortly.
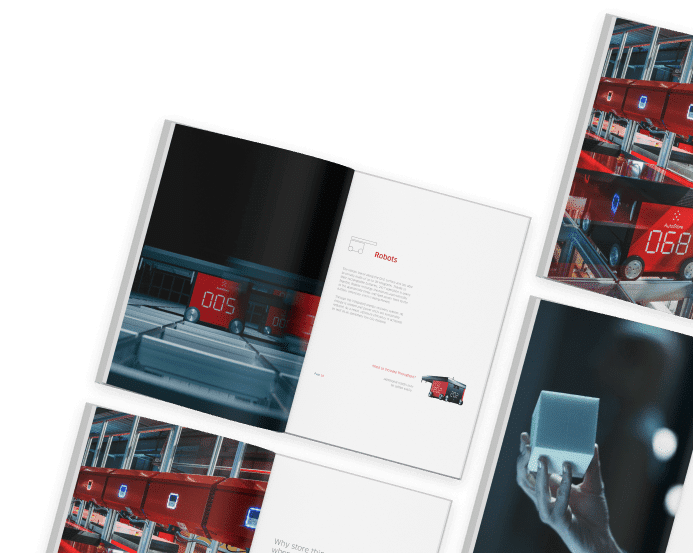
Thank you
Thank you for your registration! The requested files will be sent to you shortly.