Wiltec Transforms Logistics with AutoStore Solution
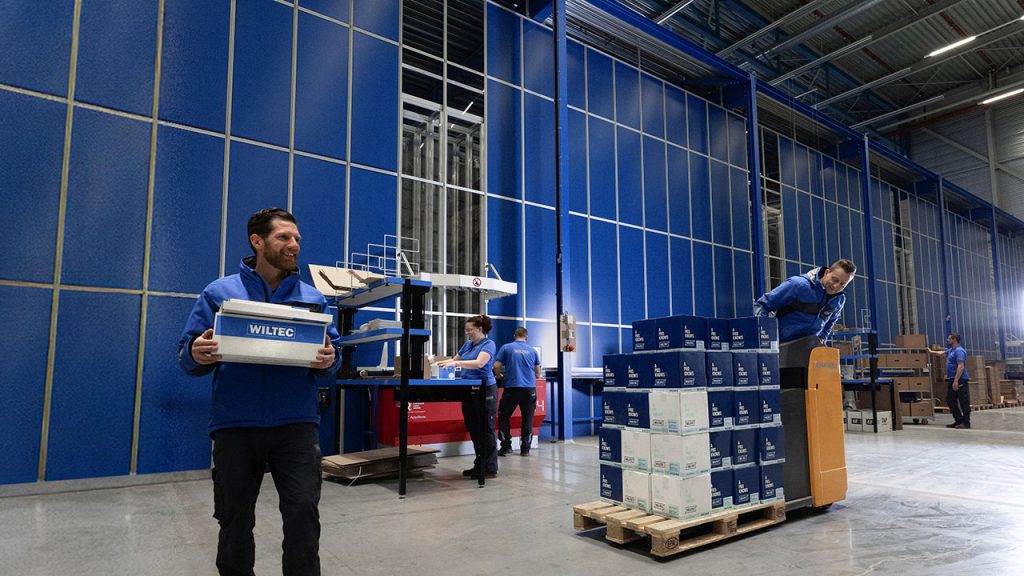
Wiltec’s Logistics Revolution
Wiltec is a leading specialist in Industrial & Spray Technology, Safety & Workwear, and Office & Facility Solutions. With their motto “Working smart and staying safe,” they help their customers work more efficiently and safely every day. Wiltec not only plays the role of supplier but also acts as a reliable supply chain coordinator, proactive advisor, and solution-oriented expert with years of experience. Together with customers, Wiltec identifies opportunities to improve business processes, work environments, and working conditions to be smarter, more efficient, and more sustainable. This way, Wiltec contributes to ongoing progress.
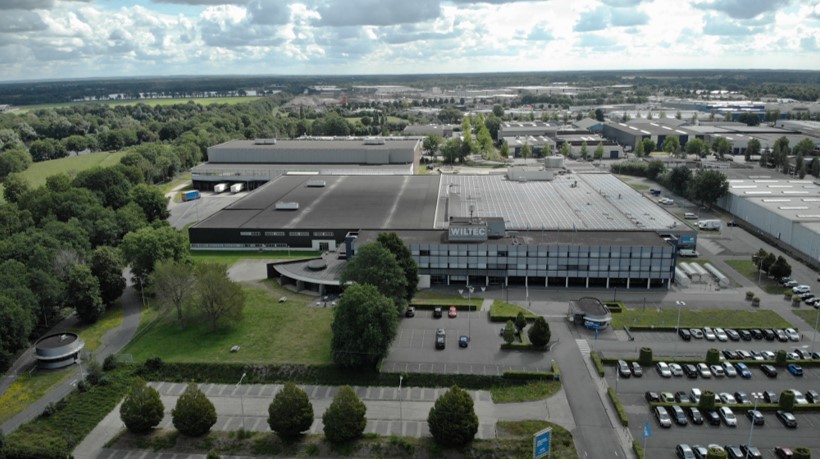
The Path to Efficient Automation
After implementing a new WMS system in previous years, Wiltec was ready to take the next step in automation. A storage and order processing system designed for the future: automated, reliable, less dependent on employee knowledge and experience, scalable storage capacity, and potential for growth and expansion. The goal: less work pressure, scalability, and improved delivery reliability and quality to better serve customers.
In early 2020, Wiltec approached the specialists at Lalesse Logistic Solutions to brainstorm a solution.
From Complexity to Innovation
Wiltec ships over 20,000 packages monthly to 42 countries. With an inventory of over 45,000 different items and more than 1,100 brands, the challenge of same-day order fulfillment and rapid customer service was significant.
Before the introduction of AutoStore, orders were collected manually through employee walkthroughs of the warehouse. Growth was difficult due to space limitations. The walking distances per employee became too great, the quality of orders could not be guaranteed, and delivery speed and reliability were increasingly challenging to maintain. Given Wiltec’s rapid growth and ambitions, and the need to continue serving customers effectively, processes needed to be redesigned to be smarter and more efficient.
Smart Automation: The Perfect Solution for Wiltec’s Logistics Challenges
In close collaboration between Wiltec and Lalesse, the available data was analyzed and interpreted to gain a good understanding of the logistics flow. Because Wiltec stores not only a wide variety of products but also manages multiple customer-specific (assembly) processes, it was important to obtain insights upfront.
In the search for a future-proof logistics concept, various solutions were considered. After extensive comparison and evaluation, the AutoStore was found to be the best fit for Wiltec’s logistics operations. The system ensures: reduced dependence on personnel through automation, products come to the employee rather than the other way around, and the system makes optimal use of available space by working vertically. The system is forward-looking and flexible, scalable as Wiltec continues to grow.
With a lead time of less than a year from the award of the contract, the space-saving AutoStore automated storage and order picking solution was installed and put into use at Wiltec. After an initial start-up period, the system is now fully operational.
The AutoStore system consists of a grid with a storage capacity of 35,000 bins and features four pick and input stations on the outside. Currently, the system holds 30,000 bins with a stacking height of 16 bins. There is still room for growth within the existing grid with an additional 5,000 bins.
The compact system occupies a floor area of only 850 m2. A total of 22 robots move in two directions across the grid and can reach any position at a speed of up to 3.1 meters per second. The tasks are assigned to individual robots by the AutoStore controller via WLAN. When there are fewer tasks, or when the battery is low, the robots automatically move to one of the charging stations.
In addition to three Carousel ports and one Conveyor port for handling incoming and outgoing goods, the AutoStore system is equipped with three pre-prepared port frames for a quick expansion of pick and input capacity. Installing these frames makes it possible to add new workstations without downtime, within just a few hours.
Since each workstation is equipped with a barcode scanner and touchscreen, every station can be used for any process, offering Wiltec maximum flexibility.
The smart WCS software LogiCS, developed by Lalesse Logistic Solutions, ensures that all required order and product information is displayed to the order picker, so they know exactly what to pick from the bin. During peak times, the AutoStore system at Wiltec can execute up to 540 picks per hour.
The AutoStore system is used for storing and picking Wiltec’s smaller items. It is also used for internal orders involving assembly tasks. Each workstation is multifunctional and can handle all tasks.
Transport System for Efficient Processing
Once an employee has placed all items in the order box and the order is complete, the box is placed on the conveyor belt that runs along the workstations. The conveyor belt carries the box to the packing station, where it is then dispatched. Every box that leaves the workstation is automatically registered by LogiCS in the WMS for further processing in packing.
Faster Deliveries and Improved Efficiency
The well-coordinated intralogistics and minimal order processing time ensure that Wiltec can continue to handle the increasing number of orders, with most being shipped the same day. With the use of AutoStore, delivery reliability and speed are guaranteed, contributing to high-quality shipments and increased customer satisfaction.
Our delivery reliability—fulfilling orders as agreed with the customer—has increased again over the past year. The linked dashboards make it visible what the workload is on any given day and how it progresses throughout the day. A great result!
Peter Klaver – Operations Director
Since requested items are brought to the employees at the pick stations instead of them having to walk around the warehouse, they cover significantly fewer kilometers and can process more orders per day. Furthermore, assembling an order is less error-prone because products are automatically offered by the AutoStore. Processing speed is high, and as the physical strain is reduced, employees remain fit longer and can work more sustainably.
Our logistics colleagues used to walk between 10 and 12 kilometers per day! These distances have decreased significantly, the work is physically less demanding, and employees are much less fatigued by the end of their workday.
Jochen Nierop – Warehouse and Production Manager
The AutoStore also offers the possibility of scaling within the existing grid and used floor space.
Facts and Figures
- Area of the AutoStore system: 850 m2
- 22 AutoStore robots
- 30,000 bins
- 3 Carousel ports
- 1 Conveyor port
- Performance:
- Order picking: 180 picks per hour per workstation
- Replenishment: 100 picks per hour per workstation
Results that Matter
The AutoStore is the solution to various logistical challenges faced by Wiltec. The company can make optimal use of available space, the workflow is more efficient and time-saving, and the pressure on employees is reduced. Because the system contributes to both delivery reliability and the quality of shipped orders, Wiltec can meet customer expectations, which ultimately improves customer satisfaction. The system also offers opportunities for rapid scaling in the future.
With the implementation of AutoStore, we are better prepared for the future. We can fulfill customer commitments more efficiently, even during busy days. The quality of the order picking process is much higher than before. The system has proven to be highly reliable, helping us prepare for a tightening labor market while growing as a company. Moreover, the system, with its electric-powered robots, aligns with our sustainability goals.
Bart Zegers – Director
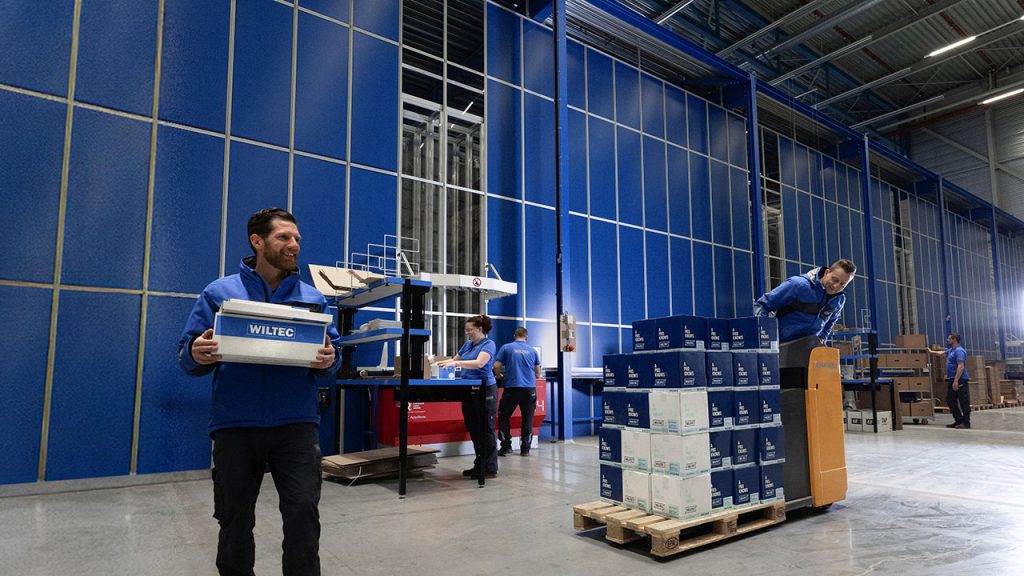
Register
Please complete the form below to access this content. One of our specialists will get in touch with you shortly.
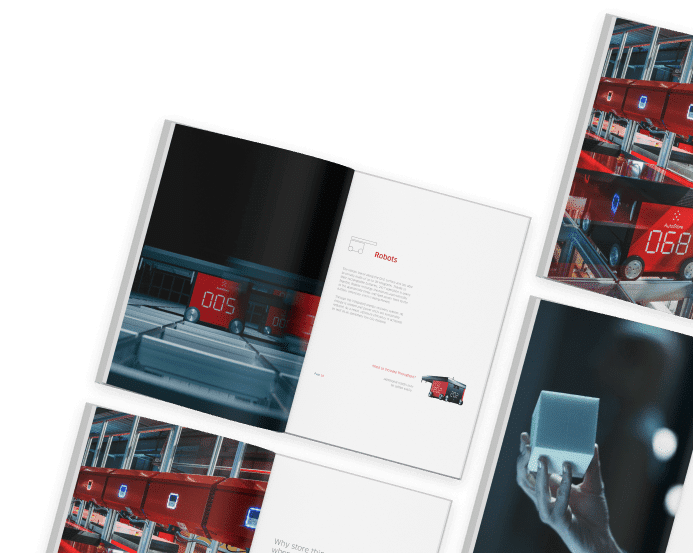
Thank you
Thank you for your registration! The requested files will be sent to you shortly.